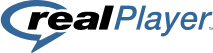
The concept of production lines is quite different from the management area, because these workshops are a logical flow. ANAST developing a tool to increase productivity lines by identifying bottlenecks and computing workloads.
It should be noted that a bottleneck is the workstation slowest chain and has the effect of blocking the flow upstream, it is interesting to highlight these items for possibly rethink their design so to make the flow smoother. The second point concerns the workload is expressed in man hours * and will impose the amount of labor in the workshop, a module is developed to smooth the load so as to engage a number of workers constant (or at least less variable).
The objective of modeling is to increase the burden of the workshop (Maximizing the number of items produced) in simulating several configurations prior to production. Results are compared and the most satisfactory configuration allows to set parameters such as the workshop production order elements, the necessary number of workers, the schedule of play ...
To analyze this problem, we use the software EM-Plant (Tecnomatix issued by) is very well suited to simulation workshops. In addition, this software is already used by sites such as Flensburger Schiffbau Gesellschaft and Meyer Werft.
Two workshops of the Chantiers de l'Atlantique-type production line is modeled by ANAST: Workshop Pre-Pre and manufacturing workshop of flat panels.
Pré-Pré fabrication Workhop
The workshop produces components smaller than 3m x 12m, in general, these floor plates, the beams, partitions, etc.. The figure represents a view of the workshop can be divided into three work areas equipped with welding robot (red). Each of these areas is separated into two blocks themselves served as raw material by individual gates (green-blue). The entrance areas of raw materials and outgoing finished components are present at the end of the workshop and two cranes (green) can handle these components.
The main requirement for optimizing the production of this workshop is the saturation of each robot welder. Configurations introduced in the modeling differ in the input sequence of constituents and the dispatching of elements to make the process islands. The best configuration is then one that saturates the robot and allows the realization of the maximum number of items.
According to this perspective, it would be necessary to run the simulation by introducing a considerable number of different combinations, therefore, a genetic algorithm was developed to create a limited set of typical configurations. The best configuration is then extracted from this limited series. It does not correspond to the optimal solution but can nevertheless increase the productivity of the workshop.